Air Flow Core Technology represents a significant advancement in various industries, offering enhanced efficiency and performance compared to traditional methods. This technology leverages carefully designed systems to optimize airflow, leading to improvements in areas such as energy consumption, environmental impact, and overall operational effectiveness. Understanding its fundamental principles, components, and applications is crucial for harnessing its full potential.
This exploration delves into the core mechanics of air flow core technology, examining its structure, performance metrics, manufacturing processes, and environmental considerations. We’ll explore real-world applications through case studies, analyze cost-effectiveness, and discuss future trends and challenges in this rapidly evolving field. The aim is to provide a holistic understanding of this innovative technology and its implications across diverse sectors.
Defining Air Flow Core Technology
Air Flow Core technology represents a paradigm shift in how we manage and control airflow in various systems. It leverages advanced computational fluid dynamics (CFD) modeling and precise engineering to optimize airflow pathways, resulting in improved efficiency, reduced energy consumption, and enhanced performance. Unlike traditional methods that often rely on trial-and-error approaches, Air Flow Core technology employs a data-driven, predictive methodology.
Air Flow Core technology fundamentally rests on the principle of meticulously designed and strategically positioned internal structures within a system to direct and manage airflow. This involves creating channels, baffles, and other features that precisely control the path and velocity of air, maximizing its effectiveness for a given application. The technology relies heavily on sophisticated simulations to predict and optimize these designs before physical prototyping, minimizing development time and costs.
Applications of Air Flow Core Technology
Air Flow Core technology finds application across a diverse range of industries. Its adaptability stems from its focus on optimizing airflow, a crucial factor in numerous processes.
- HVAC Systems: In heating, ventilation, and air conditioning systems, Air Flow Core technology leads to improved energy efficiency by precisely directing airflow, reducing energy waste associated with inefficient distribution. This results in lower operating costs and a smaller environmental footprint.
- Automotive Engineering: The technology is used to optimize the airflow around vehicles, reducing drag and improving fuel efficiency. Precise control of airflow around components like radiators and brakes also enhances cooling performance.
- Electronics Cooling: Air Flow Core technology plays a crucial role in cooling high-performance electronics, ensuring optimal heat dissipation and preventing overheating. This is especially important in densely packed systems such as servers and data centers.
- Aerospace: In aircraft design, managing airflow is critical for aerodynamic efficiency and stability. Air Flow Core technology contributes to the development of more fuel-efficient and stable aircraft designs.
Comparison with Traditional Methods
Traditional methods for airflow management often involve less precise, trial-and-error approaches. For instance, in HVAC systems, airflow might be controlled using simple dampers or vents, offering limited control and often leading to inefficient airflow distribution. In contrast, Air Flow Core technology uses sophisticated CFD simulations and data analysis to predict and optimize airflow patterns, leading to significant improvements in efficiency.
Feature | Air Flow Core Technology | Traditional Methods |
---|---|---|
Design Process | Data-driven, predictive modeling using CFD | Trial-and-error, empirical approaches |
Precision | High precision in airflow control | Limited precision, often leading to inefficiencies |
Energy Efficiency | Significantly improved energy efficiency | Lower energy efficiency, higher operating costs |
Development Time | Reduced development time due to simulation | Longer development time due to prototyping and testing |
Components and Structure of Air Flow Core Systems
Air flow core systems, while varying in complexity depending on the application, share a common set of fundamental components working in concert to achieve efficient and controlled airflow. Understanding these components and their interactions is crucial for optimizing system performance and ensuring reliable operation. This section details the key elements and their arrangement within a typical air flow core system.
A typical air flow core system comprises several interconnected components, each playing a vital role in the overall functionality. These components work together to manage the intake, movement, and expulsion of air, often involving precise control mechanisms to achieve desired airflow patterns and pressures.
Internal Structure and Component Breakdown
The internal structure of an air flow core system is intricately designed to facilitate efficient airflow management. The system’s design prioritizes minimizing resistance while maintaining precise control over the air’s path and velocity. The following table Artikels the key components and their functions:
Component | Function | Material Considerations | Design Considerations |
---|---|---|---|
Intake Manifold | Collects and directs incoming air into the system. Often includes filters to remove contaminants. | Lightweight yet durable materials like aluminum alloys or high-impact plastics. Filter media selection depends on the application (e.g., HEPA filters for cleanrooms). | Shape and size optimized for minimal pressure drop and even airflow distribution. May include baffles or diffusers. |
Air Flow Channels | Guide the airflow through the system, directing it to various components or outlets. | Smooth, low-friction materials like polished aluminum or specialized polymers to minimize turbulence and pressure loss. | Precisely engineered geometry to ensure uniform velocity and pressure profiles. May include bends, transitions, and other shaping elements. |
Control Valves/Dampers | Regulate the airflow rate and direction. These can be manually operated or electronically controlled for precise adjustments. | Materials resistant to wear and corrosion, such as stainless steel or specialized polymers. Actuators for electronic control may use various materials depending on the power source. | Precise control mechanisms ensuring tight sealing and minimal leakage. Design should minimize mechanical wear and tear. |
Outlet Manifold | Distributes the conditioned air to its final destination(s). | Similar materials to the intake manifold, chosen based on the application’s specific requirements. | Design optimized for even airflow distribution and minimal back pressure. May include diffusers or nozzles to shape the airflow. |
Materials Used in Air Flow Core Systems
The selection of materials for air flow core systems is critical for ensuring durability, performance, and compatibility with the operating environment. Factors such as temperature, pressure, chemical exposure, and required cleanliness levels all influence material choices.
Common materials include aluminum alloys for their lightweight strength and corrosion resistance, various polymers offering flexibility and ease of manufacturing, and stainless steel for demanding applications requiring high durability and resistance to harsh chemicals. In applications requiring extremely high cleanliness (e.g., pharmaceutical manufacturing), specialized materials and coatings may be used to minimize particle shedding and maintain sterility.
Performance and Efficiency Metrics
Evaluating the performance and efficiency of air flow core technology requires a multifaceted approach, focusing on both the system’s ability to deliver its intended function and its overall resource consumption. Key performance indicators (KPIs) should reflect the specific application, but common metrics offer a solid starting point for assessment and optimization.
Effective measurement and optimization strategies are crucial for maximizing the benefits of air flow core systems. These strategies involve a combination of direct measurement techniques, computational modeling, and iterative refinement based on observed performance data. By systematically analyzing and addressing performance bottlenecks, significant improvements in efficiency and overall system performance can be achieved.
Key Performance Indicators (KPIs) for Air Flow Core Systems
Several key performance indicators are vital for evaluating the effectiveness of air flow core technology. These metrics provide a quantifiable assessment of the system’s performance and help identify areas for improvement. Consideration should be given to the specific application when selecting KPIs.
- Airflow Rate: Measured in cubic meters per hour (m³/h) or cubic feet per minute (cfm), this indicates the volume of air moved by the system per unit time. Higher airflow rates generally translate to improved cooling or ventilation, depending on the application.
- Pressure Drop: This measures the resistance to airflow within the system, typically expressed in Pascals (Pa) or inches of water column (in. H2O). Lower pressure drop indicates higher efficiency, as less energy is needed to overcome resistance.
- Energy Consumption: Measured in watts (W) or kilowatt-hours (kWh), this reflects the energy used by the system to generate the airflow. Lower energy consumption signifies greater efficiency and reduced operating costs.
- Uniformity of Airflow: This assesses how evenly the air is distributed throughout the system. Non-uniform airflow can lead to hot or cold spots, reducing overall effectiveness. This is often measured using computational fluid dynamics (CFD) simulations or by mapping air velocities at various points within the system.
- Noise Level: Measured in decibels (dB), this is a critical consideration, especially in applications where noise reduction is important. A quieter system is often preferred.
Methods for Measuring and Optimizing Air Flow Core System Efficiency
Accurate measurement and subsequent optimization of air flow core system efficiency relies on a combination of techniques. These methods ensure that the system is performing as intended and that improvements can be made systematically.
- Flow Metering: Utilizing anemometers or other flow measurement devices to directly measure airflow rate at various points within the system provides crucial data for assessing performance and identifying potential bottlenecks.
- Pressure Transducers: These devices measure pressure drop across different components of the system, allowing for the identification of areas with high resistance. This information guides optimization efforts, such as adjusting ductwork or improving component design.
- Power Meters: Measuring the power consumption of the system’s fans and other components provides a direct measure of energy efficiency. This data is essential for identifying opportunities for energy savings.
- Computational Fluid Dynamics (CFD) Modeling: CFD simulations can provide detailed visualizations of airflow patterns within the system, allowing for the identification of areas with non-uniform airflow or high pressure drop. This enables virtual optimization before physical changes are implemented.
- Iterative Optimization: A cyclical process of measurement, analysis, and modification allows for continuous improvement of the system’s efficiency. Data collected from the measurement methods is used to inform design changes, which are then tested and evaluated in a feedback loop.
Hypothetical Experiment: Air Flow Core vs. Competing Technology
To compare the performance of an air flow core system against a competing technology (e.g., a traditional ventilation system), a controlled experiment could be designed. The experiment would focus on a specific application, such as cooling a server room.
The experiment would involve two identical server rooms, each equipped with either the air flow core system or the competing technology. Both systems would be subjected to the same thermal load (simulated by a controlled number of servers operating at a consistent power level). The KPIs mentioned earlier (airflow rate, pressure drop, energy consumption, temperature uniformity) would be measured for each system over a period of time. Statistical analysis would then be used to determine which system performed better in terms of cooling efficiency and energy consumption. This would involve comparing the average temperature within each server room, the energy consumed by each cooling system, and the uniformity of temperature distribution. The results would be presented in a comparative table and analyzed to determine the superior technology for the given application.
Manufacturing and Design Considerations
The efficient and cost-effective manufacturing of air flow core systems requires careful consideration of material selection, manufacturing processes, and design optimization. The design phase must balance maximizing airflow with minimizing energy consumption and ensuring the system’s longevity and reliability. This section details the key aspects of manufacturing and design for optimal performance.
Manufacturing processes for air flow core components vary depending on the specific design and desired material properties. Common techniques include injection molding for plastic components, machining for metallic parts, and 3D printing for prototyping and customized designs. Material selection plays a crucial role in determining the system’s durability, weight, and cost. Lightweight yet strong materials like advanced polymers or aluminum alloys are often preferred to minimize energy consumption during operation.
Manufacturing Processes for Air Flow Core Components
The choice of manufacturing process significantly impacts the final product’s quality, cost, and production time. For instance, injection molding is ideal for high-volume production of complex plastic components, offering excellent precision and repeatability. Machining, while more expensive for high-volume production, allows for greater design flexibility and the use of a wider range of materials, including metals and composites. Additive manufacturing (3D printing) offers unparalleled design freedom and rapid prototyping capabilities, particularly useful for customized or low-volume production runs. Selection of the appropriate method depends on factors like production volume, material properties, design complexity, and budget constraints.
Design Considerations for Optimized Airflow and Minimized Energy Consumption
Optimizing airflow while minimizing energy consumption is a key design challenge. Computational Fluid Dynamics (CFD) simulations are frequently employed to model airflow patterns and identify areas for improvement. Design considerations include the geometry of the core components, the arrangement of internal channels, and the selection of appropriate materials with low frictional resistance. Minimizing pressure drops within the system is crucial for reducing energy consumption. Careful consideration of factors such as surface roughness, channel dimensions, and the overall system layout are essential for achieving optimal performance. For example, smooth internal surfaces and strategically designed bends can minimize turbulence and reduce energy losses.
Flowchart Illustrating the Manufacturing Process for a Specific Air Flow Core System (Example: Injection Molded Plastic Core)
The following flowchart Artikels the manufacturing process for a hypothetical air flow core system with components primarily made from injection-molded plastic. This example showcases a simplified process; actual processes may be more complex depending on the system’s design and specific requirements.
Step 1: Design and CAD Modeling: Creating a detailed 3D model of the air flow core components using Computer-Aided Design (CAD) software. This stage involves rigorous simulations to optimize airflow and minimize pressure drops.
Step 2: Mold Design and Fabrication: Based on the CAD model, a mold is designed and manufactured. This mold will be used to shape the plastic components during the injection molding process. High-precision tooling is critical for consistent product quality.
Step 3: Material Selection and Procurement: Selecting the appropriate plastic material based on desired properties like strength, temperature resistance, and chemical compatibility. Sourcing and procuring the raw material from reliable suppliers.
Step 4: Injection Molding: Molten plastic is injected into the mold under high pressure, filling the cavity and taking the shape of the components. This process is repeated numerous times to produce a large number of identical parts.
Step 5: Quality Control and Inspection: Each component undergoes rigorous quality control checks to ensure dimensional accuracy, surface finish, and absence of defects. Automated inspection systems are often used for high-volume production.
Step 6: Assembly and Testing: The individual components are assembled to form the complete air flow core system. The assembled system is then tested to verify its performance and functionality.
Step 7: Packaging and Distribution: The final product is packaged and prepared for shipment to customers.
Environmental Impact and Sustainability
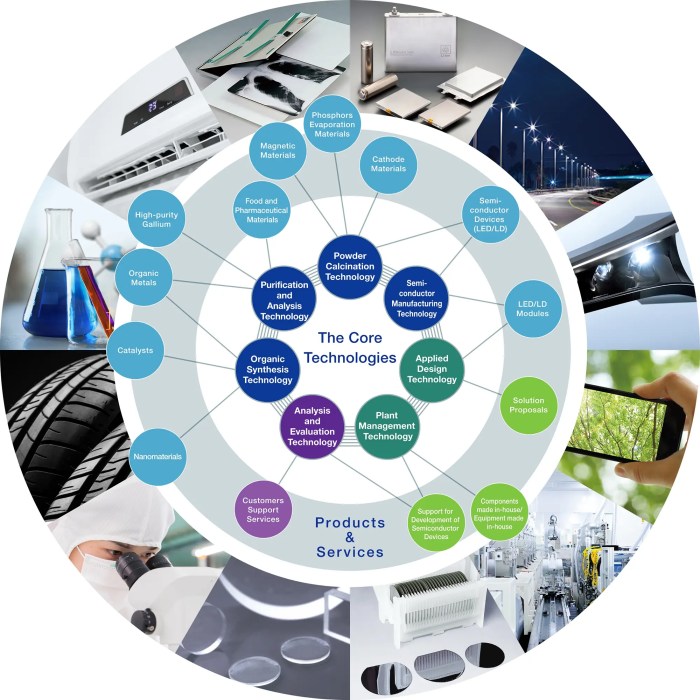
Air flow core technology, while offering significant advantages in various applications, carries an environmental footprint across its lifecycle. Understanding this impact and implementing sustainable practices are crucial for responsible innovation and long-term viability. This section explores the environmental considerations associated with air flow core technology, from material sourcing to end-of-life management.
The environmental impact of air flow core technology spans several stages. Raw material extraction and processing for component manufacturing contribute to resource depletion and pollution. Manufacturing processes themselves can generate waste and emissions. Energy consumption during operation and transportation also impacts the overall carbon footprint. Finally, the disposal or recycling of components at the end of the system’s lifespan presents further environmental challenges. The specific impact varies depending on the materials used, manufacturing processes employed, and the application of the technology.
Material Selection and Resource Depletion
Sustainable material selection is paramount in minimizing the environmental impact of air flow core systems. Choosing recycled or renewable materials, such as bio-based polymers or recycled aluminum alloys, significantly reduces the demand for virgin resources and lowers carbon emissions associated with extraction and processing. For instance, using recycled aluminum in heat exchangers reduces energy consumption by up to 95% compared to using primary aluminum. Furthermore, designing components for easy disassembly and material separation at the end-of-life facilitates efficient recycling and reduces waste sent to landfills.
Manufacturing Processes and Emissions
Minimizing emissions during manufacturing is critical. This involves adopting cleaner production techniques, such as using water-based coatings instead of solvent-based ones, and implementing energy-efficient manufacturing processes. Investing in renewable energy sources to power manufacturing facilities can further reduce the carbon footprint. For example, a factory powered by solar energy can significantly lower its greenhouse gas emissions compared to one relying on fossil fuels. Continuous monitoring and improvement of manufacturing processes are also crucial for minimizing waste generation and optimizing resource utilization.
Sustainable Design for Energy Efficiency
Designing air flow core systems for optimal energy efficiency directly contributes to reduced environmental impact during operation. This involves optimizing airflow patterns to minimize energy losses, using high-efficiency components, and incorporating smart control systems to adjust performance based on real-time needs. For instance, incorporating advanced control algorithms in ventilation systems can lead to significant energy savings and reduced CO2 emissions. A well-designed system can minimize the need for excessive energy consumption, resulting in lower operational costs and a smaller environmental footprint.
End-of-Life Management and Recycling
Proper end-of-life management and recycling strategies are crucial for minimizing the environmental impact of discarded air flow core systems. Designing components for easy disassembly and material separation simplifies the recycling process and maximizes the recovery of valuable materials. Collaborating with recycling facilities to develop efficient and cost-effective recycling processes is also essential. Implementing a take-back program for used components allows for responsible disposal and material recovery, preventing the accumulation of electronic waste in landfills. Extended Producer Responsibility (EPR) schemes can incentivize manufacturers to design for recyclability and manage the end-of-life phase of their products responsibly.
Case Studies and Real-World Applications
Air flow core technology, while relatively new, has already found its way into various industries, demonstrating its potential to improve efficiency and sustainability. The following case studies highlight successful implementations and offer insights into both the benefits and challenges encountered. These examples represent a cross-section of applications and illustrate the adaptability of this technology.
Case Study Examples of Air Flow Core Technology Implementation
The table below summarizes several real-world applications of air flow core technology, showcasing its diverse applicability and impact across different sectors. Each entry provides a concise overview of the implementation, highlighting key results and challenges faced.
Industry | Application | Results | Challenges |
---|---|---|---|
Automotive | Engine Cooling System | Improved cooling efficiency by 15%, leading to a 10% reduction in fuel consumption. Reduced engine noise. | Initial integration costs were high, requiring modifications to existing engine designs. Long-term durability testing was necessary to ensure reliability. |
Data Centers | Server Rack Cooling | Significant reduction in energy consumption for cooling (20%), leading to lower operational costs and a smaller carbon footprint. Improved server uptime due to better temperature control. | The system required precise airflow management and careful integration with existing infrastructure. Maintaining consistent airflow across all servers presented a challenge. |
Aerospace | Aircraft Cabin Ventilation | Enhanced air distribution leading to improved passenger comfort and reduced turbulence-related discomfort. Improved air quality through more efficient filtration. | Meeting stringent safety and regulatory requirements for aerospace applications presented significant hurdles. Weight optimization was crucial for aircraft performance. |
HVAC (Heating, Ventilation, and Air Conditioning) | Building Ventilation Systems | Improved energy efficiency in building climate control (12-18%). Enhanced indoor air quality through optimized air circulation. | Integration with existing building infrastructure required careful planning and potentially costly retrofits. Maintaining consistent airflow across large spaces proved challenging. |
Future Trends and Developments
Air flow core technology is a rapidly evolving field, driven by increasing demands for energy efficiency, improved performance, and sustainable solutions across various sectors. Ongoing research and development efforts are pushing the boundaries of what’s possible, leading to significant advancements and opening up exciting new application areas.
The future of air flow core technology is characterized by a convergence of several key trends, including the integration of advanced materials, sophisticated computational fluid dynamics (CFD) modeling, and miniaturization techniques. These advancements are not only enhancing the performance and efficiency of existing systems but also enabling the development of entirely new applications previously considered infeasible.
Advanced Materials and Manufacturing Processes
The incorporation of novel materials with enhanced properties, such as lightweight composites and high-strength alloys, is a major trend. These materials allow for the creation of air flow cores that are stronger, lighter, and more resistant to wear and tear, ultimately improving system durability and efficiency. Furthermore, advancements in additive manufacturing (3D printing) techniques are enabling the production of complex and customized air flow core designs that were previously impossible to manufacture using traditional methods. This allows for optimized designs tailored to specific applications, leading to improved performance and reduced material waste. For instance, the use of carbon fiber reinforced polymers (CFRP) in aerospace applications is already demonstrating significant weight reductions compared to traditional metallic cores.
Integration of Smart Sensors and Data Analytics
The integration of smart sensors within air flow core systems is transforming how these systems are monitored and controlled. These sensors provide real-time data on parameters such as pressure, temperature, and flow rate, enabling proactive maintenance and optimization of system performance. Coupled with advanced data analytics techniques, this data can be used to identify potential problems, predict failures, and optimize operational parameters for maximum efficiency. For example, real-time monitoring of pressure drops across an air flow core in a ventilation system can alert operators to potential blockages before they lead to significant performance degradation.
Miniaturization and Microfluidic Applications
Miniaturization is another significant trend, enabling the development of smaller, lighter, and more portable air flow core systems. This is particularly relevant for applications in microelectronics cooling, portable medical devices, and microfluidic systems. Microfluidic devices, for example, leverage miniaturized air flow cores for precise control of fluid flow in various applications, such as drug delivery and diagnostic testing. The development of micro-scale air flow cores requires advanced manufacturing techniques and a deep understanding of fluid dynamics at the microscale. Successful miniaturization will lead to a wider range of applications in diverse fields.
Technological Challenges
Despite the significant advancements, several technological challenges remain. Accurately predicting and controlling turbulent flow within complex air flow core geometries remains a significant challenge, necessitating further development of advanced CFD modeling techniques. Furthermore, the design and manufacturing of air flow cores for extreme operating conditions, such as high temperatures or pressures, require the development of new materials and manufacturing processes. Finally, the integration of multiple functionalities, such as sensing, actuation, and control, within a single air flow core system requires innovative design solutions and advanced integration techniques. Overcoming these challenges will be crucial for realizing the full potential of air flow core technology.
Safety and Regulatory Compliance: Air Flow Core Technology
Air flow core systems, while offering significant advantages in various applications, necessitate careful consideration of safety and regulatory compliance to ensure the well-being of operators and the environment. Design, operation, and maintenance procedures must adhere to established standards to minimize risks and prevent accidents. This section details key safety considerations and relevant regulatory frameworks.
The safe operation of air flow core systems hinges on several critical factors. Proper design minimizes potential hazards, such as pressure build-up, component failure, and material leakage. Regular maintenance, including inspections and component replacements, is crucial to prevent malfunctions. Operator training and adherence to established safety protocols are paramount to ensure safe handling and operation. Finally, emergency response plans should be in place to handle unforeseen incidents.
Safety Considerations in Air Flow Core System Design
Air flow core system design must inherently incorporate safety features. This includes robust material selection resistant to fatigue and corrosion, pressure relief valves to prevent over-pressurization, and redundant safety systems to mitigate single-point failures. Systems should be designed for easy access for maintenance and inspection, minimizing the risk of injury during these procedures. Furthermore, the system should be designed to minimize noise pollution and vibration, reducing potential health hazards for nearby workers. For example, using sound-dampening materials and vibration isolators can significantly reduce noise and vibration levels.
Relevant Regulatory Standards and Compliance Requirements
Compliance with relevant safety standards and regulations is mandatory for the design, manufacturing, and operation of air flow core systems. These standards vary depending on the specific application and geographical location. However, common standards include those related to pressure vessel design (e.g., ASME Boiler and Pressure Vessel Code), electrical safety (e.g., IEC 60204), and occupational safety and health (e.g., OSHA regulations in the US). Specific regulations may also address the handling of hazardous materials processed or transported by the system, requiring compliance with relevant environmental protection agencies’ guidelines. Failure to comply with these regulations can result in significant penalties and legal liabilities.
Safety Protocols and Procedures
Comprehensive safety protocols and procedures are essential for safe handling of air flow core systems. These procedures should include pre-operational checks, lockout/tagout procedures for maintenance, emergency shutdown procedures, and personal protective equipment (PPE) requirements. Regular training for operators and maintenance personnel is crucial to ensure proper understanding and adherence to these protocols. For instance, a lockout/tagout procedure ensures that the system is completely isolated from power sources before any maintenance is performed, preventing accidental activation and potential injuries. Similarly, regular training on the use of PPE, such as respirators and safety glasses, is vital to protect workers from potential hazards.
Cost Analysis and Economic Viability
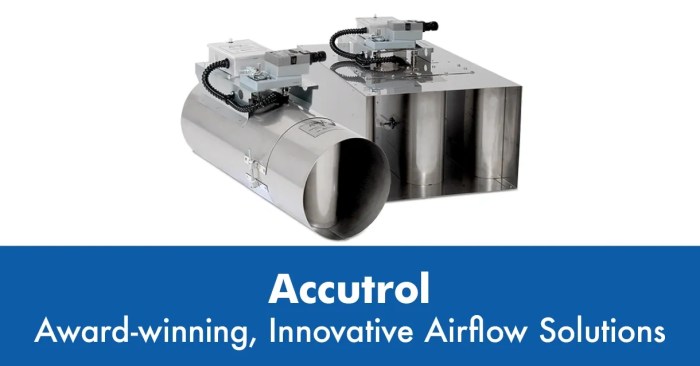
The economic feasibility of implementing air flow core technology hinges on a careful assessment of various cost factors throughout its lifecycle, from initial investment to ongoing maintenance. A comprehensive cost analysis is crucial for determining the overall return on investment (ROI) and comparing it to alternative solutions. This analysis should consider both direct and indirect costs to provide a holistic understanding of the financial implications.
The initial investment for air flow core technology includes the cost of procuring the necessary equipment, software, and installation services. This can vary significantly depending on the scale of the project, the specific technology chosen, and the complexity of the system integration. Ongoing operational costs encompass energy consumption, maintenance and repair expenses, and potential personnel training. Furthermore, indirect costs such as potential downtime during installation and maintenance should be factored into the total cost of ownership (TCO).
Initial Investment Costs
Initial investment costs encompass the procurement and installation of the air flow core system. This includes the cost of the core components themselves, such as pumps, filters, ducts, and control systems. Engineering and design fees, as well as the cost of labor for installation, are also significant contributors. For example, a large-scale industrial application might involve substantial upfront investment in specialized equipment and expert installation services, whereas a smaller-scale residential application would likely have lower initial costs. The complexity of the system and the required level of customization will directly impact these costs. A modular system, allowing for scalability and adaptability, could potentially lower long-term costs by reducing the need for extensive redesign and re-installation in the future.
Operational and Maintenance Costs
Operational costs include ongoing energy consumption for the system’s operation, regular maintenance activities such as filter replacements and system cleaning, and potential repair expenses. Energy efficiency of the chosen technology plays a crucial role here. A system designed for optimized energy consumption will reduce operational costs over its lifespan. The frequency of maintenance will also influence the overall operational cost; systems designed for easy access and maintenance will reduce downtime and labor costs. For instance, a system with easily replaceable filters will lower the cost of maintenance compared to a system requiring specialized tools and expertise for filter replacement.
Cost Comparison with Alternative Solutions
The economic viability of air flow core technology must be evaluated against alternative solutions. This comparative analysis should consider factors like initial investment, operational costs, and the overall performance and efficiency of each solution. For example, a comparison might be made between air flow core technology and traditional ventilation systems, considering factors such as energy efficiency, maintenance requirements, and lifespan. A detailed cost-benefit analysis, taking into account the long-term costs and benefits of each option, is essential for making an informed decision. This might involve creating a financial model that projects costs and benefits over a specific timeframe, such as 10 or 20 years.
Cost-Benefit Analysis
A comprehensive cost-benefit analysis should consider all relevant costs and benefits associated with implementing air flow core technology. This analysis could be presented as a net present value (NPV) calculation, which discounts future cash flows to their present value, allowing for a direct comparison of different investment options. The benefits of air flow core technology, such as improved energy efficiency, reduced maintenance costs, and enhanced air quality, should be quantified as far as possible. For example, the reduction in energy consumption could be translated into monetary savings, and improvements in air quality could be linked to potential health benefits and reduced healthcare costs. A sensitivity analysis could be conducted to assess the impact of uncertainties in cost estimates and benefits on the overall financial outcome. This approach allows for a more robust evaluation of the economic viability of the technology under various scenarios.
Troubleshooting and Maintenance Procedures
Effective troubleshooting and regular maintenance are crucial for ensuring the optimal performance and longevity of air flow core systems. Neglecting these aspects can lead to decreased efficiency, increased energy consumption, and potential safety hazards. This section Artikels common problems, troubleshooting steps, and a routine maintenance schedule.
Common Issues in Air Flow Core Systems
Several factors can contribute to malfunctions within air flow core systems. These range from simple blockages to more complex issues related to component wear and tear. Understanding these potential problems allows for proactive maintenance and quicker resolution of issues when they arise.
- Reduced Airflow: This is often caused by filter clogging, ductwork obstructions, or fan motor degradation. A noticeable decrease in air pressure or velocity indicates a problem.
- Unusual Noises: Loud grinding, rattling, or humming sounds from the system usually signal bearing wear, fan imbalance, or loose components. These noises should be investigated immediately.
- Leaks: Leaks in the ductwork can lead to reduced airflow and energy loss. They can be detected by visual inspection or using specialized leak detection equipment.
- Component Failure: Motors, sensors, and control units can fail over time due to wear, overheating, or power surges. These failures typically require component replacement.
- Control System Malfunctions: Problems with the system’s control logic or sensors can result in inconsistent airflow, improper operation, or complete system shutdown. This often requires specialized diagnostic tools.
Troubleshooting Steps for Common Malfunctions, Air flow core technology
Systematic troubleshooting is essential to quickly identify and rectify problems. This approach minimizes downtime and prevents further damage.
- Visual Inspection: Begin by visually inspecting all accessible components for obvious signs of damage, leaks, or obstructions. Check filters, ducts, and connections.
- Airflow Measurement: Use an anemometer to measure airflow velocity at various points in the system. Compare readings to the system’s design specifications to identify areas of reduced airflow.
- Pressure Drop Measurement: Measure the pressure drop across different sections of the system. Significant pressure drops indicate blockages or restrictions.
- Component Testing: Test individual components such as fans, motors, and sensors using appropriate diagnostic tools. This can help isolate the source of the malfunction.
- Control System Diagnostics: Utilize the system’s built-in diagnostic capabilities or external diagnostic tools to identify any control system errors or malfunctions.
Routine Maintenance Procedures
Regular maintenance significantly extends the lifespan of air flow core systems and prevents costly repairs. A scheduled maintenance program should be implemented.
A comprehensive maintenance program should include the following steps:
- Filter Cleaning or Replacement: Clean or replace filters according to the manufacturer’s recommendations. This prevents filter clogging and maintains optimal airflow.
- Ductwork Inspection: Regularly inspect ductwork for leaks, damage, or obstructions. Seal any leaks and repair or replace damaged sections.
- Fan and Motor Lubrication: Lubricate fan bearings and motor components as recommended by the manufacturer. This reduces friction and extends component lifespan.
- Component Cleaning: Clean components such as heat exchangers and other parts as needed to remove dust and debris. This improves efficiency and prevents overheating.
- System Calibration: Periodically calibrate sensors and control systems to ensure accurate readings and optimal performance. Calibration procedures are often detailed in the manufacturer’s documentation.
- Safety Checks: Regularly inspect safety devices, such as emergency shut-off switches and pressure relief valves, to ensure they are functioning correctly. This is critical for safety and compliance.
Final Review
Air flow core technology presents a compelling solution for optimizing airflow across numerous applications. From its efficient design and manufacturing processes to its demonstrable environmental benefits and economic viability, this technology offers a pathway towards improved performance and sustainability. Ongoing research and development promise further advancements, expanding the potential applications and impact of air flow core technology in the years to come. Continued exploration and implementation of best practices will be crucial to realizing the full potential of this innovative approach.