Adhesive joining of structural components: new insights and technologies represent a significant advancement in engineering and manufacturing. This field, traditionally overshadowed by more established methods like welding and bolting, is experiencing a renaissance driven by the development of novel adhesive chemistries and a deeper understanding of surface science. This exploration delves into the advantages, challenges, and future directions of adhesive bonding, examining its impact across diverse industries.
From the historical context of adhesive use in structural applications to the cutting-edge advancements in nanocomposites and self-healing materials, we will cover the spectrum of adhesive technologies. We will also discuss critical aspects like surface preparation, joint design optimization, and rigorous quality control procedures. The ultimate goal is to provide a comprehensive overview of this rapidly evolving field and highlight its potential to revolutionize structural engineering.
Introduction to Adhesive Joining
Adhesive joining, a method of fastening materials using a bonding agent, has evolved significantly from its early applications to become a prominent technique in various structural applications. While traditional methods like welding and bolting remain important, adhesive bonding offers distinct advantages and is increasingly used in diverse industries, from aerospace to construction. This section provides a historical overview, explores the benefits, and addresses the limitations of adhesive joining in structural contexts.
Adhesive bonding in structural applications has a surprisingly long history, though its widespread adoption is a relatively recent phenomenon. Early forms of adhesive bonding used natural materials like resins and gums. However, the development of synthetic polymers in the 20th century revolutionized the field, leading to the creation of high-strength, durable adhesives capable of withstanding significant stress. The aerospace industry, driven by the need for lightweight and strong components, was a key driver in this development, pushing the boundaries of adhesive technology and leading to the creation of specialized adhesives for demanding applications. The increasing use of composite materials further propelled the growth of adhesive joining, as these materials often lend themselves well to bonding techniques.
Advantages of Adhesive Joining
Compared to traditional methods like welding and bolting, adhesive joining offers several key advantages. These advantages often translate to improved performance and reduced costs in many applications. For instance, adhesive bonding can distribute stresses more evenly across a joint, leading to increased fatigue resistance and improved overall strength in some cases. Furthermore, it avoids the localized stress concentrations that can occur with bolted or welded joints. This is particularly beneficial in applications where vibration or cyclical loading is a concern. Another significant advantage is the ability to join dissimilar materials, something that can be challenging or impossible with other joining methods. This opens up design possibilities that were previously unavailable. Finally, adhesive bonding often results in a lighter structure, as it eliminates the need for bulky fasteners and reduces the amount of material required in some designs.
Limitations and Challenges of Adhesive Bonding
Despite its advantages, adhesive bonding also faces certain limitations and challenges. One major concern is the susceptibility of adhesives to environmental factors such as temperature, humidity, and chemicals. Exposure to extreme temperatures or certain solvents can degrade the adhesive’s properties, weakening the bond and potentially compromising the structural integrity of the joined components. Another challenge is the need for precise surface preparation. The adhesive must make intimate contact with the surfaces to be joined, and any contamination or imperfections can significantly reduce bond strength. This requirement often necessitates careful cleaning and surface treatment before bonding. Finally, the relatively long curing times required for some adhesives can increase manufacturing lead times and limit production efficiency. This needs to be carefully factored into the design and manufacturing process. Accurate prediction of long-term performance can also be complex, necessitating robust testing and analysis to ensure reliability and safety.
Types of Adhesives for Structural Applications
The selection of an appropriate adhesive is crucial for the success of any structural bonding application. The performance and longevity of the bonded joint depend heavily on the adhesive’s inherent properties and its compatibility with the materials being joined. This section will explore the key characteristics of several common structural adhesive types, allowing for a more informed decision-making process during design and implementation. Understanding the strengths and limitations of each type is paramount to achieving optimal bond strength, durability, and cost-effectiveness.
Structural adhesives offer a versatile alternative to traditional joining methods like welding or bolting, often providing superior strength and flexibility in specific applications. They are broadly categorized based on their chemical composition and resulting properties. Three major types – epoxy, acrylic, and polyurethane – will be compared and contrasted below, highlighting their suitability for various structural applications.
Comparison of Structural Adhesive Types
The following table summarizes the key characteristics of epoxy, acrylic, and polyurethane adhesives, providing a comparative overview to aid in selection. Note that these are general characteristics, and specific product properties can vary significantly depending on the manufacturer and formulation.
Adhesive Type | Strength | Durability | Cost | Application Method |
---|---|---|---|---|
Epoxy | High strength, excellent shear and tensile strength | High, resistant to many chemicals and environmental factors | Moderate to High | Two-part mixing, various application methods (brush, syringe, automated dispensing) |
Acrylic | Moderate to High strength, good impact resistance | Good, susceptible to some solvents and UV degradation | Moderate | One-part or two-part systems, often applied via brush or spray |
Polyurethane | Moderate strength, excellent flexibility and impact resistance | Good, resistant to moisture and some chemicals | Low to Moderate | One-part or two-part systems, various application methods (spray, brush, roller) |
Adhesive Selection Flowchart
Choosing the right adhesive requires careful consideration of several factors. The following flowchart provides a visual guide to navigate the selection process based on application-specific requirements. The process begins with defining the essential characteristics needed for the application and progresses through a series of decision points to narrow down the most suitable adhesive type.
Adhesive joining offers exciting advancements in structural engineering, allowing for lighter, stronger components. The potential for improved traceability and verification of materials used in these processes is significant, and understanding how this could be achieved is key; for instance, exploring how a system could use what is blockchain technology to ensure material authenticity and quality could revolutionize the industry.
This would ultimately lead to more reliable and robust adhesive joining of structural components.
[Imagine a flowchart here. The flowchart would start with a box labeled “Application Requirements Defined?”. If yes, it branches to “Strength Requirements (High, Moderate, Low)?”, leading to separate paths for each strength level. Each strength level then branches to “Durability Requirements (High, Moderate, Low)?”, again with separate paths for each level. Finally, each combination of strength and durability leads to a recommended adhesive type (Epoxy, Acrylic, or Polyurethane), with a final box indicating the “Selected Adhesive”. If the initial question is “No”, the flowchart would loop back to define the application requirements.]
Advances in adhesive joining offer exciting possibilities for stronger, lighter structural components, impacting various fields. The precision required mirrors that of surgical procedures, and considering the financial aspects, a quick look at surgical technology starting pay highlights the skilled labor involved in such precise work. This parallels the specialized expertise needed to optimize adhesive bonding for structural integrity, demanding both advanced materials and meticulous application techniques.
Surface Preparation and Pretreatment Techniques
Achieving strong, durable adhesive bonds in structural applications hinges critically on proper surface preparation. The quality of the bond is directly proportional to the surface energy and cleanliness of the materials being joined. Contaminants, such as oils, greases, oxides, and other residues, can significantly weaken the adhesive’s ability to wet and adhere to the substrate, leading to premature failure. Therefore, meticulous surface preparation is a non-negotiable step in ensuring the long-term integrity of the adhesive joint.
Surface preparation encompasses a range of techniques aimed at removing contaminants and modifying the surface topography to enhance adhesion. These techniques can be broadly classified into cleaning methods and surface treatments. Cleaning methods focus on removing loose particles and contaminants, while surface treatments aim to improve the surface energy and create a more mechanically interlocking surface. The choice of method depends on the substrate material, the type of adhesive used, and the specific application requirements.
Surface Cleaning Methods
Effective cleaning is the foundational step in any surface preparation process. This involves removing visible dirt, dust, grease, and other contaminants that can interfere with adhesive bonding. Common methods include solvent cleaning, using appropriate solvents like acetone or isopropyl alcohol; abrasive cleaning, such as using brushes or scouring pads; and ultrasonic cleaning, which uses high-frequency sound waves to dislodge particles. The selection of a cleaning method depends on the nature and level of contamination. For instance, solvent cleaning is effective for removing oily residues, while abrasive cleaning is better suited for removing heavier deposits. Ultrasonic cleaning offers a more thorough and consistent clean, particularly for complex geometries. It’s crucial to ensure complete drying after cleaning to prevent the reintroduction of contaminants or the formation of moisture films that could negatively impact adhesion.
Surface Treatment Methods
Beyond cleaning, surface treatments aim to enhance the surface’s ability to bond with the adhesive. These methods often modify the surface chemistry or topography. For instance, chemical etching uses chemical solutions to roughen the surface and increase its surface area, thereby promoting mechanical interlocking with the adhesive. Sandblasting employs high-velocity abrasive particles to create a roughened surface, increasing the surface area and improving adhesion. Plasma treatment utilizes ionized gases to clean and activate the surface, enhancing its wettability and promoting better adhesive bonding. Flame treatment involves briefly exposing the surface to a flame, which removes contaminants and modifies the surface chemistry. The choice of surface treatment depends on the substrate material and desired level of surface modification.
Comparison of Surface Preparation Techniques
Technique | Effectiveness | Limitations |
---|---|---|
Solvent Cleaning | Effective for removing oils and greases; relatively simple and inexpensive. | May not remove all contaminants; may damage certain substrates; requires proper solvent selection and disposal. |
Abrasive Cleaning | Effective for removing heavy deposits; can create a rough surface for improved mechanical interlocking. | Can damage the substrate surface if not carefully controlled; generates dust and waste. |
Ultrasonic Cleaning | Thorough and consistent cleaning; suitable for complex geometries. | Can be expensive; may not be suitable for all materials. |
Chemical Etching | Increases surface area and improves wettability; effective for many metals. | Can be corrosive; requires careful control of etching parameters; may produce hazardous waste. |
Sandblasting | Creates a rough surface for improved mechanical interlocking; effective for a wide range of materials. | Can damage the substrate if not carefully controlled; generates dust and waste; requires specialized equipment. |
Plasma Treatment | Cleans and activates the surface; enhances wettability and adhesion. | Can be expensive; requires specialized equipment; may not be suitable for all materials. |
Flame Treatment | Removes contaminants and modifies surface chemistry; relatively fast and simple. | Can damage certain substrates if not carefully controlled; may produce harmful byproducts. |
Joint Design and Geometry
The geometry of an adhesive joint significantly impacts the strength, durability, and overall performance of the bonded assembly. Careful consideration of joint design is crucial for achieving reliable and long-lasting structural adhesive bonds. Optimizing joint geometry involves balancing factors such as stress distribution, surface area, and the susceptibility to stress concentrations.
Joint design directly influences stress distribution within the adhesive layer. Poorly designed joints can lead to localized stress concentrations, resulting in premature adhesive failure. Conversely, well-designed joints promote even stress distribution, maximizing the adhesive’s load-bearing capacity and extending the lifespan of the bonded structure. This section will explore various joint geometries and their impact on adhesive bond performance.
Lap Joints
Lap joints are characterized by the overlapping of two adherends. This configuration is simple to manufacture and widely used in various applications. However, the stress distribution in a lap joint is not uniform; higher stress concentrations occur at the edges of the overlap. A simple lap joint involves two plates overlapping. Imagine two rectangular metal plates, each 10cm x 5cm, overlapping by 5cm. The stress concentration is highest at the edges of the overlap, leading to potential failure initiation at these points. Increasing the overlap length reduces stress concentration but increases the overall weight and material cost. Modifications like using tapered overlaps or adding reinforcing elements can improve the performance of simple lap joints.
Butt Joints
Butt joints involve the direct end-to-end joining of two adherends. They offer a clean aesthetic but are inherently weaker than lap joints due to their smaller surface area and increased susceptibility to shear stresses. A butt joint, unlike a lap joint, doesn’t offer the same surface area for adhesive bonding. Consider two identical square wooden blocks joined end-to-end. The small contact area makes this joint prone to failure under significant stress. Reinforcement, such as adding a filler material or using a thicker adhesive layer, can improve the joint’s strength. However, these modifications can also introduce additional complexities in manufacturing.
Scarf Joints
Scarf joints are characterized by an angled overlap between two adherends. This design helps distribute stress more evenly across the adhesive layer compared to lap joints, leading to improved strength and durability. A scarf joint, in contrast to a butt joint, provides a larger effective adhesive surface area. Visualize two wooden planks with angled edges joined together, forming a longer, continuous piece. The angled surface increases the contact area and effectively disperses the stress, thereby increasing the joint’s strength. The angle of the scarf joint influences the stress distribution; a gentler angle leads to better stress distribution but requires a longer overlap. The optimal angle depends on the materials used and the anticipated load.
Optimizing Joint Geometry for Specific Applications
The design process for optimizing joint geometry involves considering the specific application’s requirements, material properties, and loading conditions. Finite element analysis (FEA) is a powerful tool used to simulate stress distribution within different joint geometries and predict failure modes. For example, in aerospace applications, where lightweight construction is paramount, scarf joints are often preferred due to their high strength-to-weight ratio. In contrast, lap joints might be more suitable for simpler applications requiring ease of manufacturing. The choice of adhesive also influences the joint design; higher strength adhesives allow for smaller overlap lengths in lap joints, resulting in compact designs. Material selection is also a critical factor; the compatibility of the adhesive with the adherends is crucial for achieving a strong and durable bond.
Advanced Adhesive Technologies
The field of adhesive joining has seen significant advancements, moving beyond traditional epoxy and cyanoacrylate systems. Innovative technologies are now offering superior performance characteristics, opening new possibilities for structural applications demanding enhanced strength, durability, and functionality. This section explores some of these cutting-edge adhesive systems and their potential impact.
Advanced adhesive technologies leverage nanoscale materials and novel chemical formulations to achieve properties unattainable with traditional adhesives. This leads to lighter, stronger, and more adaptable structures across various industries, from aerospace and automotive to construction and electronics.
Nanocomposite Adhesives
Nanocomposite adhesives incorporate nanoparticles, such as carbon nanotubes or graphene, into the adhesive matrix. These nanoparticles significantly enhance the mechanical properties of the adhesive, increasing its strength, stiffness, and toughness. The dispersion and interaction of these nanoparticles within the polymer matrix are crucial for optimal performance. For instance, carbon nanotubes can increase tensile strength by up to 50%, while graphene can improve thermal conductivity and electrical properties. This leads to adhesives suitable for high-stress applications where traditional adhesives may fail. The enhanced properties translate to more durable and reliable bonds in structural components, particularly in aerospace and automotive applications where weight reduction and improved performance are critical.
Self-Healing Adhesives
Self-healing adhesives represent a significant leap forward in adhesive technology. These materials possess the remarkable ability to repair themselves after damage, extending the lifespan of bonded components. This self-healing capability is typically achieved through microcapsules containing a healing agent embedded within the adhesive matrix. When a crack forms, the microcapsules rupture, releasing the healing agent which then reacts to fill the crack and restore the adhesive’s integrity. For example, a self-healing epoxy containing dicyclopentadiene (DCPD) monomer can effectively seal cracks upon exposure to heat, restoring a significant portion of the original bond strength. This technology is particularly valuable in applications where repairs are difficult or costly, such as in remote locations or within complex structures.
Comparative Analysis of Traditional and Advanced Adhesive Systems
Property | Traditional Adhesives (e.g., Epoxy) | Advanced Adhesives (e.g., Nanocomposites, Self-Healing) |
---|---|---|
Tensile Strength | Moderate | High to Very High |
Toughness | Moderate | High |
Durability | Moderate; susceptible to environmental degradation | High; enhanced resistance to environmental factors |
Self-Healing Capability | None | Present in self-healing systems |
Cost | Relatively Low | Relatively High |
The table highlights the superior performance metrics of advanced adhesive systems compared to their traditional counterparts. While the initial cost may be higher, the increased durability and lifespan often lead to overall cost savings in the long run, especially when considering maintenance and repair costs.
Applications of Advanced Adhesive Technologies in Structural Components
Advanced adhesive technologies are finding increasing use in a wide array of structural applications. Nanocomposite adhesives are being incorporated into aerospace components to reduce weight while maintaining structural integrity. Self-healing adhesives are being explored for use in infrastructure applications, such as bridges and buildings, to extend the lifespan of these structures and reduce maintenance needs. In the automotive industry, these adhesives are improving the durability and performance of vehicle components, contributing to enhanced safety and fuel efficiency. Furthermore, advanced adhesives are playing a crucial role in the development of next-generation electronics, enabling the creation of more robust and reliable devices. For example, the use of self-healing adhesives in flexible electronics allows for increased resilience against mechanical stress and damage.
Testing and Quality Control of Adhesive Bonds
Ensuring the structural integrity and longevity of adhesive joints is paramount. Rigorous testing and quality control are essential to guarantee the reliability and performance of bonded components, particularly in critical applications. These processes verify that the adhesive bond meets specified requirements and performs as expected under anticipated service conditions.
Testing the strength and durability of adhesive bonds involves a range of methods designed to simulate real-world stresses. The choice of test depends on the intended application and the type of stress the joint will experience. Accurate and consistent testing is vital for both product quality and liability reasons. Understanding these methodologies is critical for engineers and manufacturers involved in adhesive bonding.
Tensile and Shear Testing Methods
Tensile testing measures the strength of an adhesive bond under tension, pulling the bonded components apart in a direction perpendicular to the bonding surface. This method is commonly used to determine the tensile strength of the adhesive joint, expressed in units of force per unit area (e.g., MPa or psi). Shear testing, on the other hand, assesses the strength of the bond under shear forces, where the bonded surfaces slide past each other. Different shear test configurations exist, such as lap shear, where overlapping components are pulled parallel to the bond line, and T-peel testing, where a bonded film is peeled apart. These tests provide valuable data on the adhesive’s ability to withstand various types of stress. For example, a lap shear test might be used to evaluate the strength of an adhesive used in a structural beam, while a T-peel test could be applied to assess the performance of an adhesive in a flexible packaging application. The results of these tests are compared against predetermined specifications to ensure the bond meets the required strength criteria.
Best Practices for Ensuring Quality and Reliability
Maintaining consistent quality in adhesive bonding requires meticulous attention to detail throughout the entire process. This begins with careful selection of the appropriate adhesive for the specific application and materials being joined, considering factors such as temperature resistance, chemical resistance, and the expected load. Proper surface preparation is critical to ensure optimal adhesion. This includes cleaning the surfaces to remove contaminants like grease, oil, and dust, and often involves surface treatments like priming or etching to enhance surface energy and promote better bonding. Precise control of the adhesive application process is also crucial, ensuring uniform coverage and the correct adhesive thickness. Finally, curing conditions must be carefully controlled to achieve the desired bond strength and properties. Adherence to established procedures and consistent monitoring of the process are vital for maintaining quality and minimizing variability.
Quality Control Measures and Standards
A comprehensive quality control program is essential for ensuring consistent bond quality. This typically involves:
- Regular inspections of materials and equipment: This ensures that the adhesives and substrates are within specifications and that equipment is properly calibrated and maintained.
- Process monitoring and documentation: This includes recording key process parameters, such as temperature, pressure, and curing time, to ensure consistency.
- Statistical process control (SPC): SPC techniques are used to monitor process variability and identify potential problems before they lead to defects.
- Destructive testing of sample joints: This involves testing a representative sample of bonded joints to verify that they meet specified strength and durability requirements.
- Non-destructive testing (NDT): Methods such as ultrasonic testing or radiography can be used to inspect bonds without causing damage, allowing for the assessment of larger populations.
- Adherence to relevant industry standards: Following established standards, such as those provided by ASTM International or ISO, provides a framework for ensuring consistent quality and performance.
Applications in Different Industries
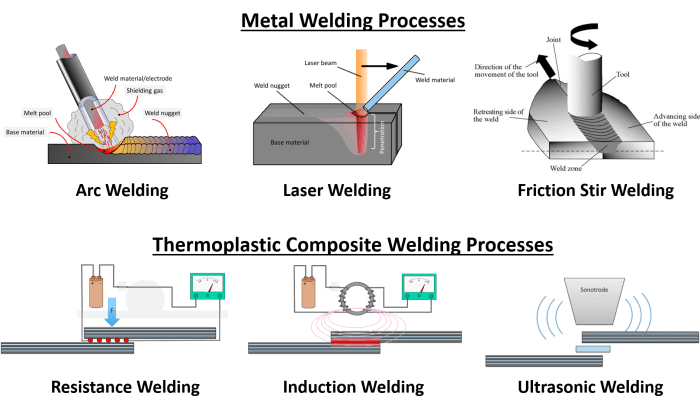
Adhesive bonding has revolutionized manufacturing across numerous sectors, offering lightweight, strong, and often cost-effective solutions compared to traditional joining methods like welding or riveting. The specific adhesive requirements, however, vary significantly depending on the operating environment and performance demands of each industry. This section will explore the diverse applications of adhesive joining in aerospace, automotive, and construction, highlighting the critical considerations in adhesive selection and joint design for optimal performance and reliability.
The choice of adhesive and joint design is crucial for achieving the desired performance characteristics in each industry. Factors such as temperature resistance, chemical resistance, shear strength, and fatigue resistance are paramount, and the selection process often involves rigorous testing and analysis. Furthermore, the complexity of the joint design can significantly impact the overall strength and reliability of the bond.
Aerospace Applications of Adhesive Joining
The aerospace industry demands exceptionally high performance and reliability from its materials and joining methods. Adhesive bonding is frequently employed in aircraft construction due to its ability to create lightweight, strong, and aerodynamically efficient structures. For instance, adhesives are used to bond composite materials, such as carbon fiber reinforced polymers (CFRPs), which are crucial for reducing aircraft weight and improving fuel efficiency. These applications require adhesives with exceptional temperature resistance to withstand extreme temperature fluctuations during flight, as well as high strength and durability to maintain structural integrity under significant stress. Specific examples include bonding honeycomb structures in aircraft wings and fuselages, and attaching various components within the aircraft interior. The selection of the adhesive is driven by factors like the specific composite material, the required bond strength, and the operating temperature range. Joint design is optimized for stress distribution and to minimize the risk of delamination or bond failure.
Automotive Applications of Adhesive Joining
In the automotive industry, adhesive bonding is increasingly used for a wide range of applications, from body panel assembly to structural bonding. The advantages include improved corrosion resistance, reduced weight, and simplified assembly processes. For example, adhesives are employed to bond automotive body panels, offering a smooth, aesthetically pleasing finish while enhancing the structural integrity of the vehicle. Other applications include bonding windshields, attaching interior components, and joining structural elements within the vehicle chassis. The adhesives used in the automotive industry must exhibit excellent durability and resistance to environmental factors like moisture, temperature changes, and UV radiation. The choice of adhesive will also depend on the specific materials being bonded (e.g., steel, aluminum, plastics), and the required bond strength and flexibility. Joint design considerations often focus on achieving a strong and consistent bond while minimizing the amount of adhesive used to reduce weight and cost.
Construction Applications of Adhesive Joining
The construction industry utilizes adhesive bonding for various applications, focusing on its ability to create strong, durable, and weather-resistant joints. Examples include bonding timber structures, attaching cladding materials, and installing insulation. In timber construction, adhesives provide a strong and reliable connection between wooden elements, often replacing traditional methods like nails or screws. This can lead to faster construction times and improved structural integrity. For cladding materials, adhesives allow for the creation of seamless and aesthetically pleasing facades. The selection of adhesives in construction is guided by factors such as the type of materials being joined, the environmental conditions (e.g., temperature, humidity), and the required load-bearing capacity. The joint design needs to consider the potential for movement and expansion due to temperature fluctuations and moisture absorption. The adhesives must be resistant to weathering, UV degradation, and potential chemical attack.
Environmental Considerations
The adhesive industry, while crucial to numerous sectors, presents significant environmental challenges throughout its lifecycle, from raw material extraction and manufacturing processes to the ultimate disposal of adhesive products and bonded components. Understanding and mitigating these impacts is crucial for achieving sustainable manufacturing and responsible consumption. This section explores the environmental footprint of adhesives, highlights eco-friendly alternatives, and examines relevant regulations and standards.
The manufacturing of many common adhesives involves volatile organic compounds (VOCs), solvents, and potentially hazardous chemicals. These substances can contribute to air pollution, impacting air quality and potentially human health. Furthermore, the energy consumption associated with production, transportation, and disposal adds to the overall carbon footprint. Disposal of adhesives and bonded materials can also present problems, particularly with adhesives that are not readily biodegradable or recyclable. Improper disposal can lead to soil and water contamination.
Eco-Friendly Adhesive Options
Several manufacturers are actively developing and marketing adhesives with reduced environmental impact. These often utilize bio-based materials, such as plant-derived oils or polymers, minimizing reliance on petroleum-based resources. Water-based adhesives, for example, significantly reduce VOC emissions compared to solvent-based counterparts. Furthermore, advancements in adhesive chemistry are leading to the development of more easily recyclable and biodegradable adhesives. These developments aim to reduce the long-term environmental burden associated with adhesive use. For instance, some adhesives are designed to be easily removed or degraded at the end of a product’s life, simplifying recycling processes and reducing waste.
Regulations and Standards for Adhesive Environmental Impact
Various national and international regulations govern the use and disposal of adhesives, focusing primarily on VOC emissions and the presence of hazardous substances. The European Union’s REACH (Registration, Evaluation, Authorisation and Restriction of Chemicals) regulation, for example, mandates the registration and assessment of chemicals used in adhesives, aiming to restrict or phase out the use of substances of very high concern (SVHCs). Similar regulations exist in other regions, often focusing on specific adhesive types or applications. In addition to regulatory frameworks, industry standards and certifications, such as those offered by various environmental organizations, provide guidelines for sustainable adhesive selection and use, promoting environmentally responsible practices within the industry. Adherence to these standards can help manufacturers and consumers make informed decisions that minimize the environmental footprint of adhesive joining.
Future Trends and Research Directions
The field of adhesive joining is experiencing a period of rapid innovation, driven by the increasing demand for stronger, lighter, and more sustainable structural components across various industries. Emerging trends are pushing the boundaries of adhesive performance, leading to exciting possibilities for improved structural integrity, reduced environmental impact, and enhanced cost-effectiveness. These advancements are fueled by ongoing research into novel adhesive chemistries, improved manufacturing processes, and a deeper understanding of the complex interfacial interactions between adhesives and substrates.
The convergence of materials science, nanotechnology, and advanced manufacturing techniques is paving the way for significant breakthroughs in adhesive technology. This is resulting in adhesives with tailored properties for specific applications, improved durability under harsh environmental conditions, and the development of more sustainable and eco-friendly alternatives to traditional adhesive systems. Research is focusing on enhancing the efficiency and precision of adhesive bonding processes, while simultaneously reducing the environmental footprint associated with adhesive production and disposal.
Bio-inspired Adhesives and Self-Healing Materials
Bio-inspired adhesives, mimicking the remarkable adhesive properties found in nature (e.g., gecko feet, mussels), offer significant potential for creating high-strength, environmentally friendly adhesives. Research is exploring the use of biopolymers and other naturally derived materials to develop adhesives with enhanced adhesion, toughness, and biodegradability. Simultaneously, the development of self-healing adhesives is gaining traction. These materials can autonomously repair minor damage, extending the lifespan of bonded structures and reducing maintenance costs. Imagine an aircraft fuselage that can automatically repair small cracks, eliminating costly repairs and improving safety. This is a significant area of research and development, with potential applications ranging from aerospace to civil engineering.
Advanced Characterization Techniques and Predictive Modeling
The ability to accurately predict the long-term performance of adhesive bonds is crucial for ensuring structural reliability. Advanced characterization techniques, such as in-situ microscopy and spectroscopy, are providing unprecedented insights into the interfacial bonding mechanisms and degradation processes within adhesive joints. This detailed understanding is facilitating the development of sophisticated predictive models, capable of simulating the behavior of adhesive bonds under various loading conditions and environmental factors. For example, finite element analysis (FEA) coupled with experimental data allows engineers to predict the lifespan of an adhesive joint under specific stress and temperature conditions, enabling more accurate design and improved safety margins.
Sustainable and Biodegradable Adhesives
Growing environmental concerns are driving the development of sustainable and biodegradable adhesives. Research is focusing on replacing petroleum-based polymers with renewable resources, such as plant-based oils and bio-derived monomers. The development of water-based adhesives and adhesives with reduced volatile organic compound (VOC) emissions is also gaining importance. The transition to these more environmentally friendly options reduces the overall environmental impact of adhesive manufacturing and disposal, contributing to a more sustainable construction and manufacturing landscape. Examples include the increasing use of soy-based adhesives in wood products and the exploration of bio-based epoxy resins.
High-Performance Adhesives for Extreme Environments
The demand for high-performance adhesives capable of withstanding extreme temperatures, pressures, and harsh chemicals is continuously increasing. Research is exploring the use of advanced polymer chemistries and nanomaterials to develop adhesives with enhanced thermal stability, chemical resistance, and mechanical strength. This is particularly relevant for applications in aerospace, automotive, and oil and gas industries, where components are exposed to challenging operational conditions. For instance, the development of adhesives capable of operating at cryogenic temperatures is crucial for space exploration and certain industrial applications. Similarly, adhesives that can withstand high temperatures are vital for high-performance engines and aerospace applications.
Case Studies of Successful Adhesive Joining Applications
Adhesive bonding has proven its efficacy in numerous large-scale projects, demonstrating its ability to replace or supplement traditional joining methods. The success of these applications hinges on a meticulous approach encompassing material selection, surface preparation, joint design, and rigorous quality control. This section details several compelling examples, highlighting the key factors contributing to their success.
Adhesive Bonding in Wind Turbine Blade Manufacturing, Adhesive joining of structural components: new insights and technologies
The manufacturing of wind turbine blades often employs adhesive bonding to join various composite materials. Large-scale blades, sometimes exceeding 100 meters in length, require robust and reliable joining techniques. Successful applications leverage high-performance epoxy adhesives, specifically formulated for the demanding environmental conditions experienced by wind turbines. Careful surface preparation, including precise cleaning and priming, is crucial to ensure optimal adhesion. The joint design itself is optimized for stress distribution, minimizing the risk of failure under cyclical loading. Rigorous quality control, including non-destructive testing methods like ultrasonic inspection, ensures the integrity of the bonded joints. The consistent use of these techniques has led to improved blade lifespan and reduced manufacturing costs.
Aircraft Fuselage Assembly using Structural Adhesives
Modern aircraft manufacturing increasingly relies on adhesive bonding for fuselage assembly. This approach allows for lighter weight structures, improved aerodynamic performance, and reduced fuel consumption. The success of adhesive bonding in this context is due to the development of high-strength, lightweight, and fatigue-resistant adhesives. Advanced joint designs, incorporating features like tapered joints and stiffeners, are employed to optimize stress distribution and minimize stress concentrations. Stringent quality control procedures, including detailed inspection and testing, ensure the integrity and reliability of the bonded joints. The use of automated dispensing systems and precise curing processes contributes to consistency and repeatability. A notable example is the use of adhesive bonding in the assembly of the Boeing 787 Dreamliner, showcasing the technology’s maturity and capability.
Automotive Applications: Adhesive Bonding in Body-in-White Construction
The automotive industry has embraced adhesive bonding for body-in-white construction, contributing to improved vehicle stiffness, reduced weight, and enhanced noise and vibration damping. The successful integration of adhesives involves the selection of appropriate adhesive systems that can withstand the stresses and strains encountered during vehicle operation. Joint design plays a critical role, optimizing the distribution of load and minimizing stress concentrations at critical points. Automated application techniques ensure consistent bond lines and high-quality joints. Quality control measures, including visual inspection and destructive testing, verify the integrity of the adhesive bonds. The use of adhesives in this context has contributed to improved fuel efficiency and enhanced safety in modern vehicles.
Civil Engineering: Adhesive Repair of Concrete Structures
Adhesive bonding has proven invaluable in the repair and strengthening of concrete structures. This approach is particularly effective in repairing cracks and damaged sections, restoring the structural integrity of aging infrastructure. High-performance epoxy adhesives, often reinforced with fibers, are used to fill cracks and restore load-carrying capacity. Careful surface preparation, including cleaning and roughening the concrete surface, is crucial for optimal adhesion. The success of these applications hinges on selecting appropriate adhesives that are compatible with the concrete substrate and can withstand the environmental conditions. The use of adhesive bonding in concrete repair has allowed for cost-effective and efficient restoration of damaged structures.
Closure: Adhesive Joining Of Structural Components: New Insights And Technologies

In conclusion, adhesive joining of structural components offers a compelling alternative to traditional fastening methods, providing significant advantages in terms of weight reduction, design flexibility, and improved performance in specific applications. While challenges remain regarding durability and environmental considerations, ongoing research and development in advanced adhesive technologies promise to further enhance the capabilities and broaden the applicability of this crucial joining technique. The future of structural bonding is undeniably bright, paving the way for lighter, stronger, and more sustainable structures across a range of industries.